2024.07.18

Mitsubishi Gas Chemical Accelerates Climate Change Action by Establishing Technology to Produce Materials from CO2
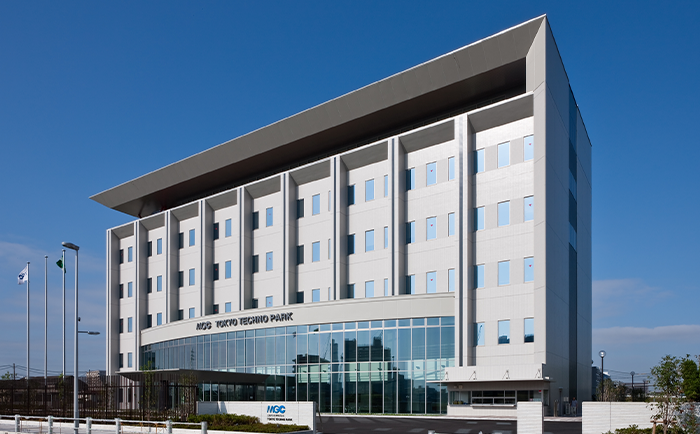
Development of Technology to Manufacture Functional Plastic Materials from CO2 Moving to Full Implementation in 2024 and Beyond under NEDO’s Green Innovation Fund
Mitsubishi Gas Chemical (MGC) proposed a project on the “Development of Technology to
Manufacture Functional Plastic Materials from CO2” in response to a call for
proposals by
the New Energy and Industrial Technology Development Organization (NEDO) under the Green
Innovation Fund. The proposal was adopted in February 2022. MGC then completed the
construction of a pilot plant at its Tokyo Research Laboratory in November 2023 to start
full-scale development of the production technology in 2024.
The Green Innovation Fund was launched under the leadership of the Ministry of Economy,
Trade and Industry with a total budget of ¥2 trillion, and began calling for proposals in
energy and other fields around the spring of 2021. One such field was “Development of
Technology for Producing Raw Materials for Plastics Using CO2 and/or Other
Sources,” for
which multiple joint research teams were selected to implement various projects.
“Development of Technology to Manufacture Functional Plastic Materials from CO2”
was among
these projects, and the research consortium formed for the project was led by Tosoh
Corporation. Its members include, in addition to MGC, the Interdisciplinary Research Center
for Catalytic Chemistry of the National Institute of Advanced Industrial Science and
Technology (AIST); Professors Keiichi Tomishige and Yasuhiro Fukushima of the Tohoku
University Graduate School of Engineering; Professor Masazumi Tamura of Osaka City
University’s Research Center for Artificial Photosynthesis; and Colcoat Co., Ltd.
The consortium obtained a total of ¥20 billion in subsidies. Tosoh and MGC will set up
research facilities at their own sites and will be responsible for process development of
raw materials for polyurethane and polycarbonate respectively. Because it is tough, clear
and lightweight, polycarbonate has wide-ranging applications and is commonly found in
automotive meter panels, cover films for game machines and smartphones, and optical lenses.
“We initially started R&D to make diphenyl carbonate, a raw material of polycarbonate, from
CO2 in 2014. Tohoku University and Nippon Steel published their findings from
basic research
in this field around that time, which led us to join their research. Since then, we have
continued joint research with many partners,” said Hidefumi Harada, who has led the
development of this production technology as Senior Research Manager of MGC’s Tokyo Research
Laboratory.
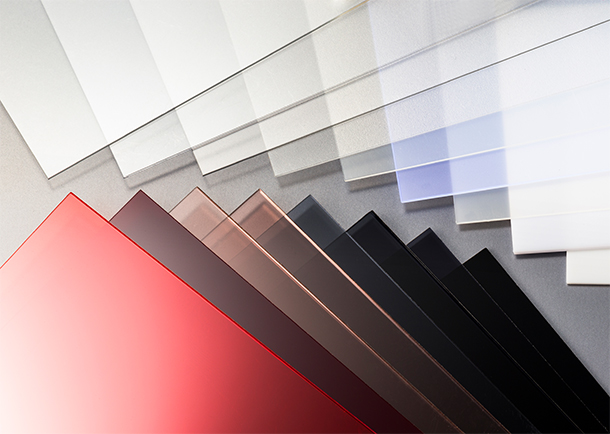
What are the advantages of making plastic materials from CO2?
You may wonder what is so impressive about this joint research. The answer is given by
Takashi Fujii, a Senior Manager for Engineering Plastics Division, Specialty Chemicals
Business Sector of MGC:
“To combat global warming, it is essential to reduce CO2 emissions, as we all
know. In this
regard, our joint research can contribute in two ways. One is by enabling the containment of
CO2 as a raw material and the production of plastic materials from it. The other
happens
during the production of diphenyl carbonate, a raw material of polycarbonate, and this is
the ability to minimize energy consumption for production, which means less CO2
emissions.”
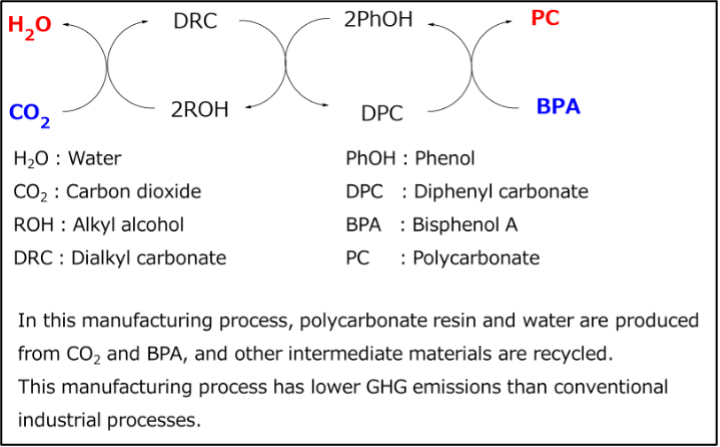
CO2 is all around us, and it is hard to transform CO2 into other
substances, as it is a
stable inorganic compound. However, MGC has successfully developed a production engineering
process that uses CO2 as a raw material. This process emits less CO2
during production and
is even cost-effective.
This achievement was derived from basic research by Tohoku University and Nippon Steel. They
discovered a catalytic reaction system and used it to succeed in making CO2 react
with
alcohol. MGC joined them, and has since striven to find ways to industrialize their basic
research results. Harada describes the efforts as follows.
“A general assumption is that converting CO2 into a chemical requires enormous
energy.
However, the process of synthesizing a carbonate compound through a reaction between
CO2 and
alcohol requires little energy because it is an equilibrium reaction that proceeds at a high
rate as long as the water produced as a by-product is efficiently removed.
Although the
process itself is energy-efficient, the challenge lies in removing the generated water from
the reaction system, which is very time- and energy-consuming.
Various companies have tried
to address this problem through R&D, with researchers racking their brains to find a
desirable way to remove water from the reaction system. Our process uses a certain organic
compound as a dehydrant to move the equilibrium reaction forward. By establishing a
technology to remove water from the dehydrant and then from the reaction system with low
energy consumption, we have successfully developed a production process for a carbonate
compound that takes place in a very short period of time, while achieving a high yield and
producing less by-product.”
After tens of thousands of attempts, a breakthrough
The team spent nearly 10 years to accomplish these research results. A key milestone was
reached in 2020 with the application of a unique technology created by MGC. That year, the
team participated in the NEDO Feasibility Study Program, and the outcome of their efforts
was praised by outside experts and MGC colleagues alike. As a result, the team won major
support from the company and joined a project under the Green Innovation Fund. Research in
the project further led to a technological breakthrough.
“Tohoku University was also working on this, but in their process, it took about 400 hours
to remove water from the reaction system. Longer time means higher cost and energy, raising
hurdles for industrialization. However, our breakthrough made it possible to remove water
from the reaction system in less than one second. We made tens of thousands of attempts
before reaching this final solution. We always valued closely observing what was happening
in the experiments to notice even the smallest phenomenon and pondering why it happened.
When the experiment succeeded, I drank a toast with the three researchers in the team,”
recalled Harada.
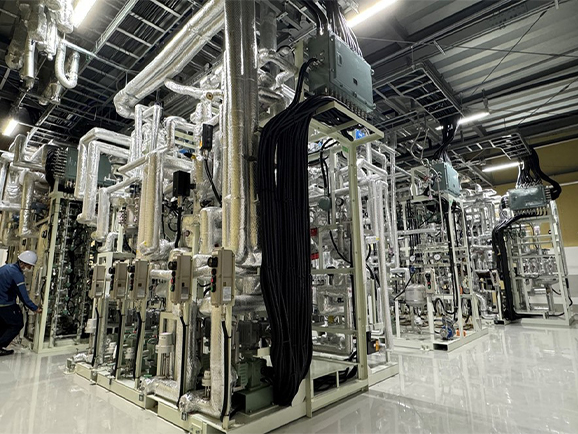
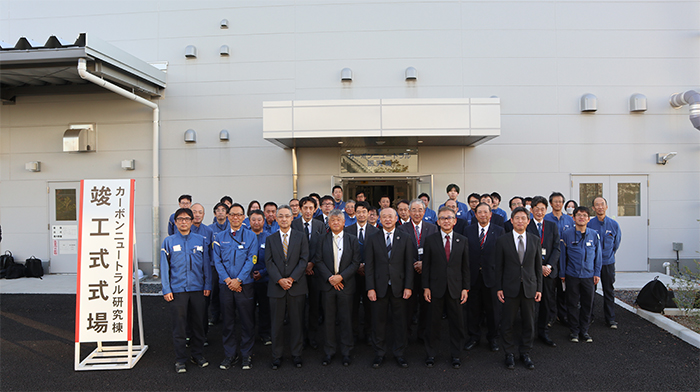
The development of this production technology is world-leading and the first of its kind in
Japan, representing an extraordinary achievement. This came at a time when it had been
suggested that the team quit, as the project had been prolonged and was struggling to earn
approval from the head office. However, Harada and his team refused to give up and
eventually attained their goal. An additional driving force behind the results was Japan’s
Carbon Neutrality Declaration, which was made in October 2020 under the Suga administration
with the goal of realizing a decarbonized society. It sets forth the target of reducing
Japan’s greenhouse gas emissions to net zero by 2050.
“The development of this production technology can have an enormous range of applications,
not only for polycarbonate but also raw materials for polyurethane and materials for
lithium-ion batteries used in electric vehicles. Going forward, we see enormous potential
for climate change applications in automotive, electricity and other fields,” says Fujii.
At the current stage of development, the fundamental issues have been resolved, and the team
is working on how to scale up the production process and how to incorporate it into the real
world.
Pursuing green innovation for future generations
MGC has strengths in four of the five major engineering plastics: polyamide, polycarbonate,
polyacetal, modified polyphenylene ether and polybutylene terephthalate. These are highly
versatile plastics, being applicable to wide-ranging items, from daily necessities to
industrial goods.
MGC made a new breakthrough in the business focused on one of them, polycarbonate. Under the
consortium, construction of a new pilot plant will begin at MGC’s factory in 2025, with
completion expected by 2027. After that, the project will move toward real-world
implementation in view of licensing and alliance formation.
“For real-world implementation, value for money needs to be considered. There are some
hurdles ahead, but we intend to overcome them,” said Fujii.
Additionally, MGC has another project adopted by the Green Innovation Fund, which involves
the methanol business. Together with its collaborators, the company is working on the
development of production technology in this field as well. This means that MGC is pursuing
two green innovations, with the other being the development of technology for producing
diphenyl carbonate, a raw material of polycarbonate.
MGC aims to eliminate the need for phosgene, a conventional raw material of plastics like
polycarbonate, from relevant production processes by 2030, thus reducing CO2
emissions from
phosgene production. The firm also strives to reduce the cost of producing polycarbonate and
other plastics in the phosgene-free processes to a level comparable to existing products,
while improving the functionality of these plastics based on the technology to convert
CO2
into a raw material for plastics production. For this purpose, MGC will conduct pilot
production of several hundred to several thousand tons of plastic per year.
“MGC has continued research to produce carbonate compounds to be used as raw materials for
polycarbonate since the late 1980s and managed to pave the way to commercialize the results.
My team and I really feel rewarded as researchers,” Harada said.
Their ultimate goal is to advance this production technology research to the development of
high-performance polycarbonate. MGC intends to develop and demonstrate specialty chemicals
manufacturing technology for polycarbonate on a commercial scale, with a view toward helping
Japan achieve carbon neutrality by 2050.
“In Japan, natural disasters are becoming more intense every year, and the recent rise in
the frequency of such disasters poses a serious concern. This year again, it is very likely
that we will see at least one natural disaster. Climate change is an imminent crisis. With
future generations in mind, we will maintain our commitment to ensure that new green
innovations will continue to emerge from the realm of the chemical industry,” said Fujii.
INTERVIEWEE
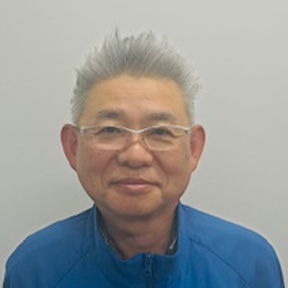
HIDEFUMI HARADA
Senior Research Manager, Tokyo Research Laboratory
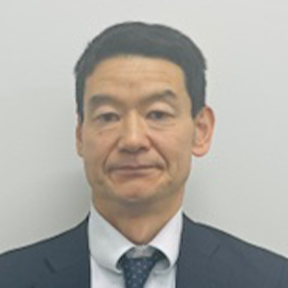
TAKASHI FUJII
Ph.D., Senior Manager, Engineering Plastics Division, Specialty Chemicals Business Sector
Mitsubishi Gas Chemical Company, Inc.
Mitsubishi Building, 5-2, Marunouchi 2-chome, Chiyoda-ku, Tokyo
Mitsubishi Gas Chemical Company, Inc. (MGC) was established in 1971 through a merger of equals between Mitsubishi Edogawa Chemical Co., Ltd., founded in 1918, and Japan Gas Chemical Co., Inc., established in 1951. MGC had a work force of 10,050 people on a consolidated basis as of the end of March 2023. While being the world’s only comprehensive methanol manufacturer, MGC holds a leading share of the global market for polycarbonate and other chemicals and operates wide-ranging businesses, offering numerous products, from basic chemicals and semiconductor-related materials to optical materials and AGELESS® free-oxygen absorbing agent.